I have a ton of pics and I'm going to post them here and there over the weekend but I have to say that the tour this time was WAY better than the tour I took in the late 1990's. I can also see why Fender is making instruments better than when I was actively selling them for a Fender dealer in the 1990's and early 2000's.
Modern Saint, Speedracer and Grover from the forum also went so I'm hoping that they share some pictures, too!
In front of the new visitors center:
a few pics from inside:
This is the "metal shop" where they use presses to punch out pickguards as well as neck plates and other metal parts like amp chassis (which is a row over). Anything that needs to be chromed is sent to an outside vendor:
Many of the machines in this area are 40-50 years old
bins of parts:
pickup bobbins
Deluxe reverbs
passing by the wood shop
neck blanks
our guide telling how they come with a little bit of milling done
an old style machine that cuts four necks at a time using a physical pattern to copy the cuts for the router. My first tour most of the machines were still like this.
Jacksons
necks getting truss rods and skunk stripes
shop fixtures for Jackson guitars
I think these are neck sanders...
installing a skunk stripe
a newer CNC machine cutting necks...this was one of the green pattern following machines the last time I was there IIRC.
Modern Saint, Speedracer and Grover from the forum also went so I'm hoping that they share some pictures, too!
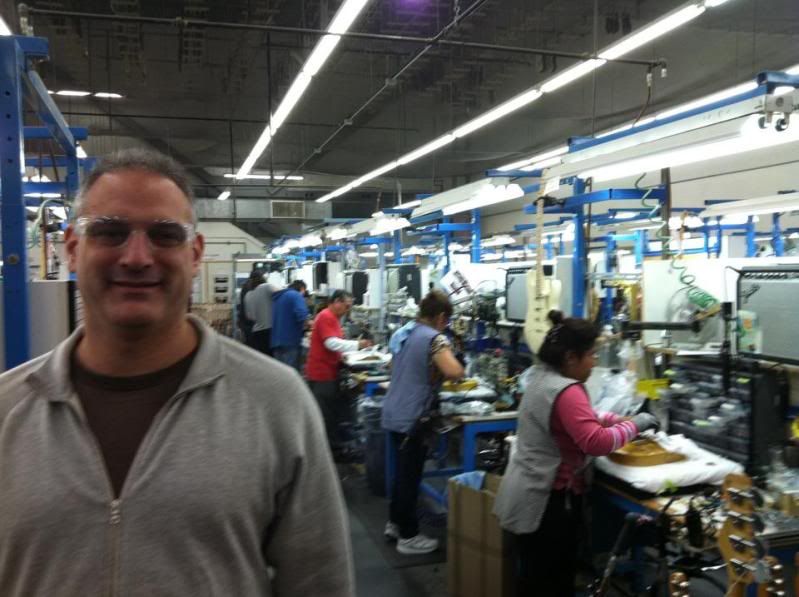
In front of the new visitors center:
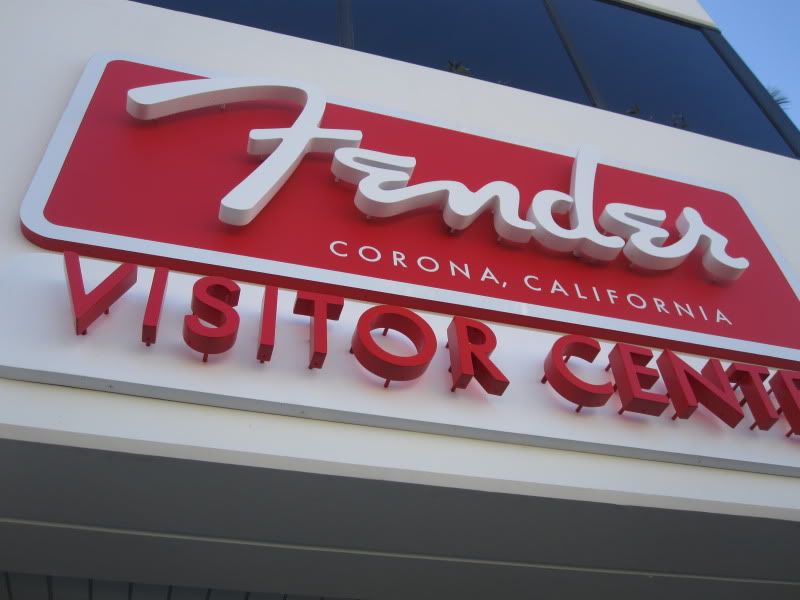
a few pics from inside:
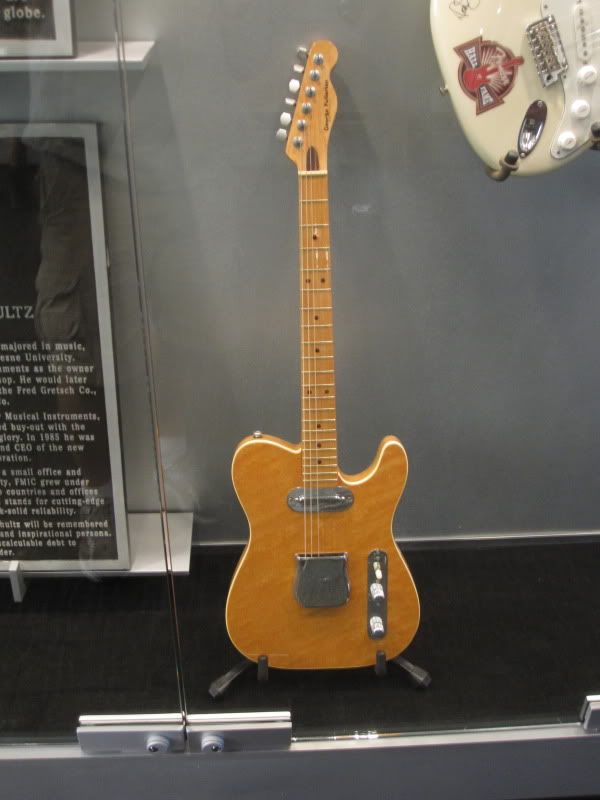
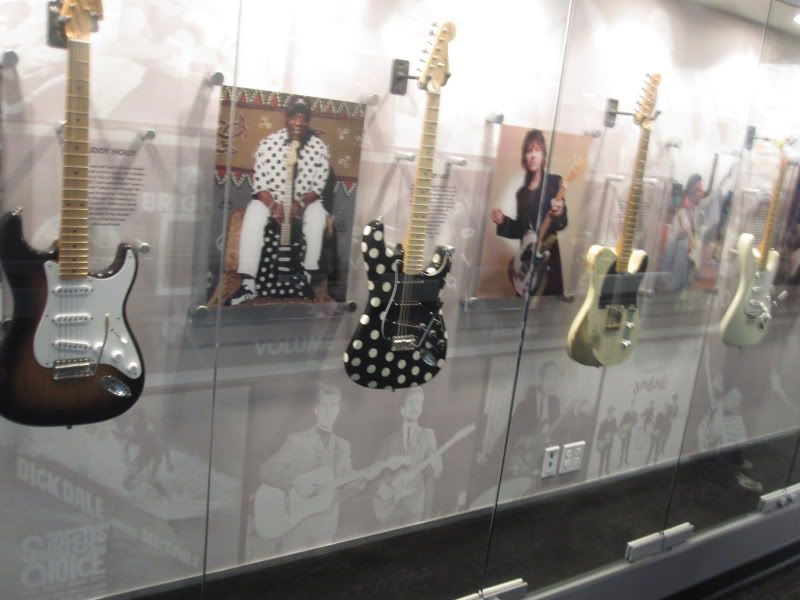
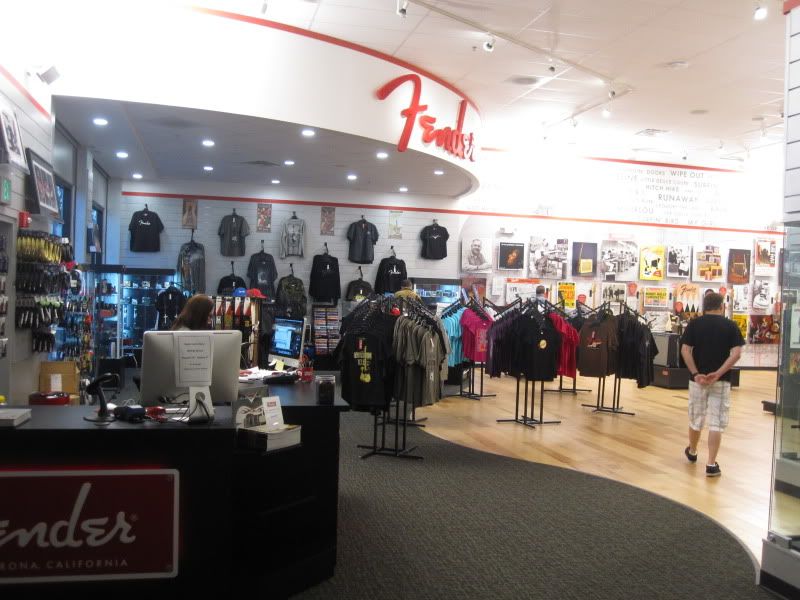
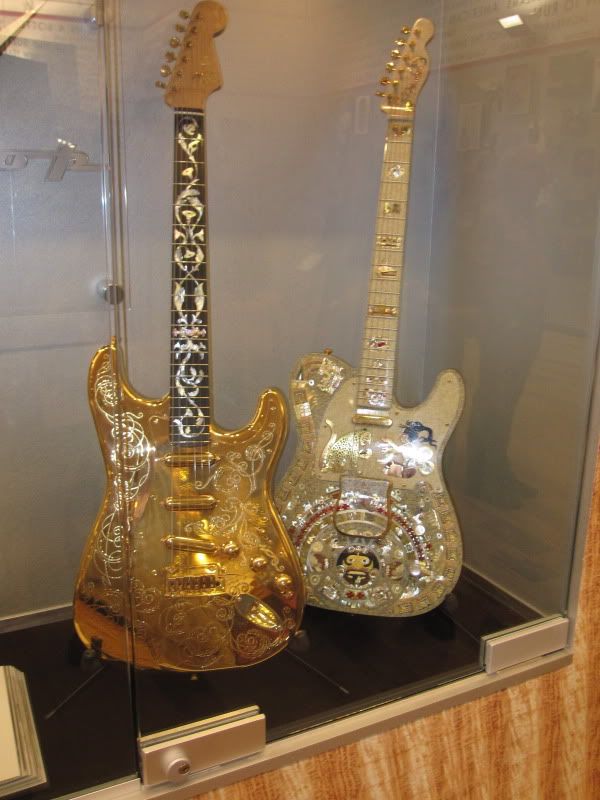
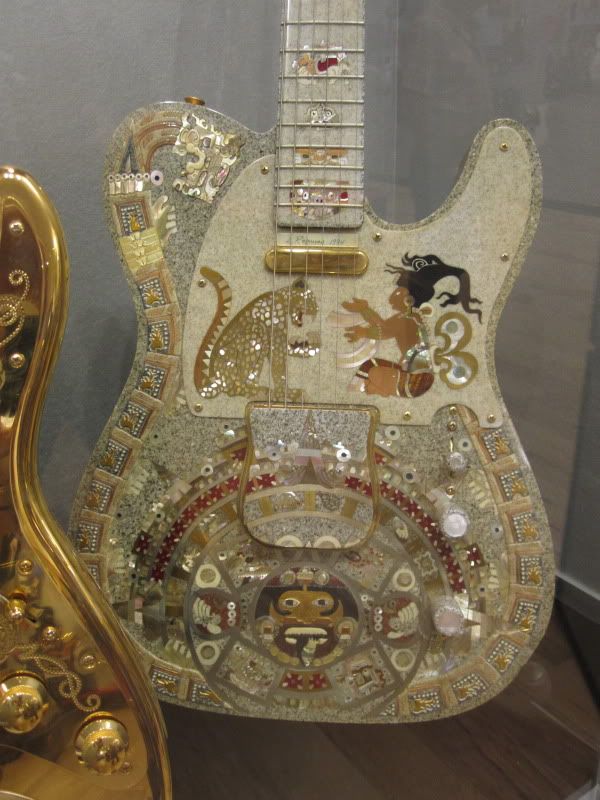
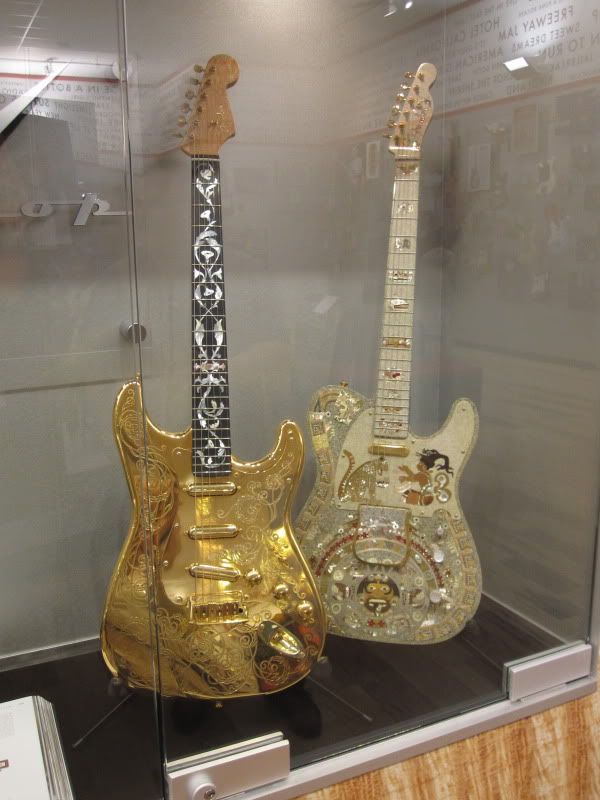
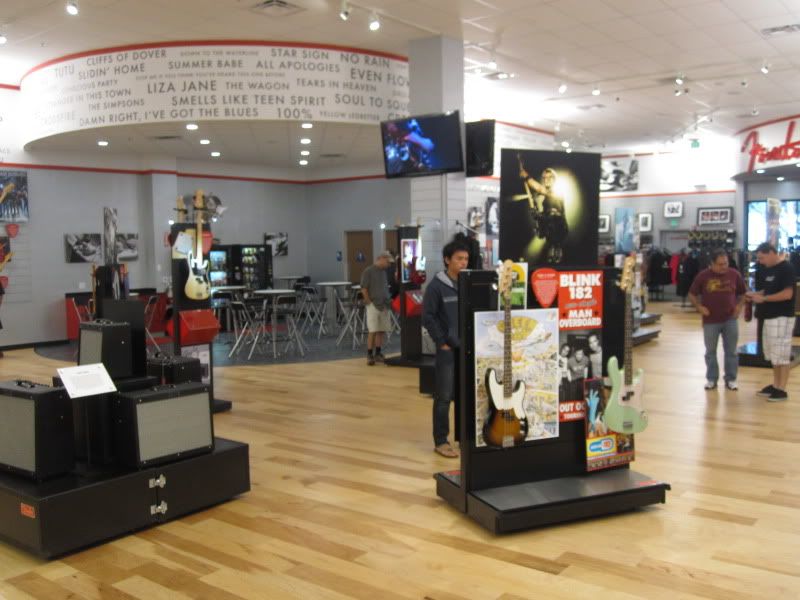
This is the "metal shop" where they use presses to punch out pickguards as well as neck plates and other metal parts like amp chassis (which is a row over). Anything that needs to be chromed is sent to an outside vendor:
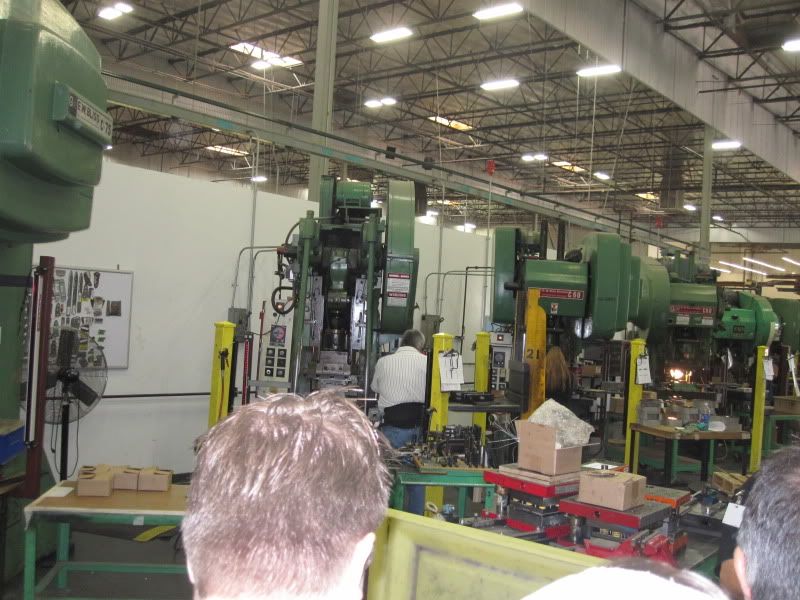
Many of the machines in this area are 40-50 years old
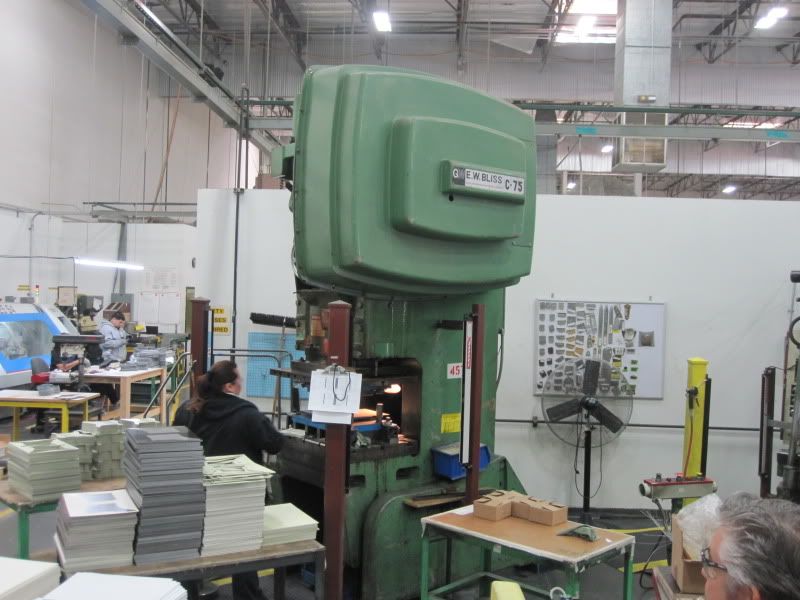
bins of parts:
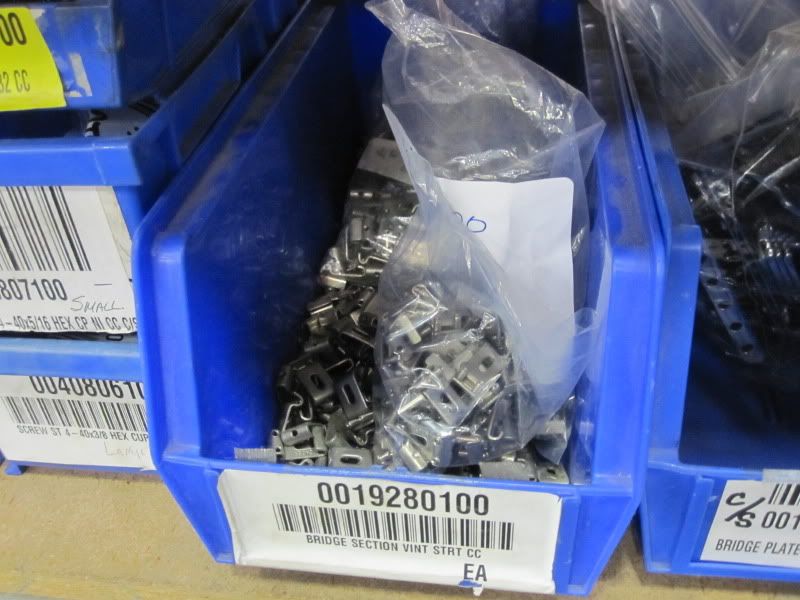
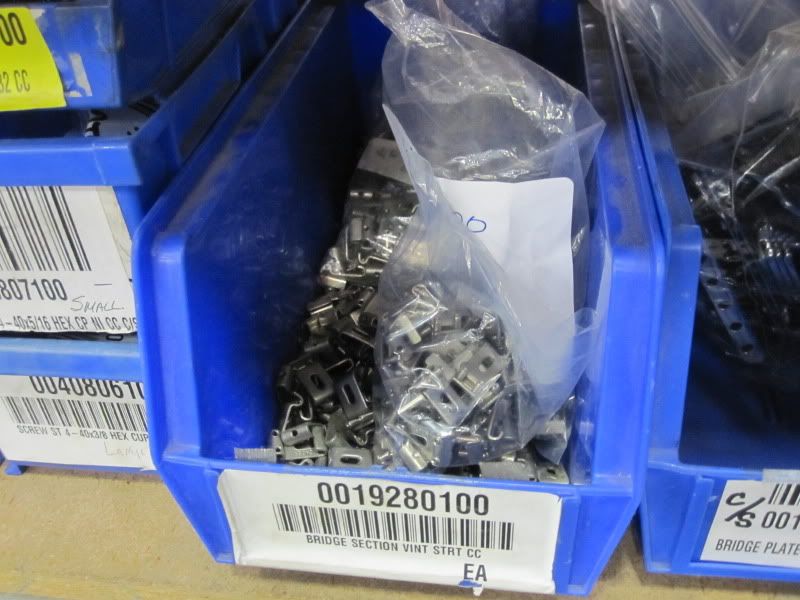
pickup bobbins
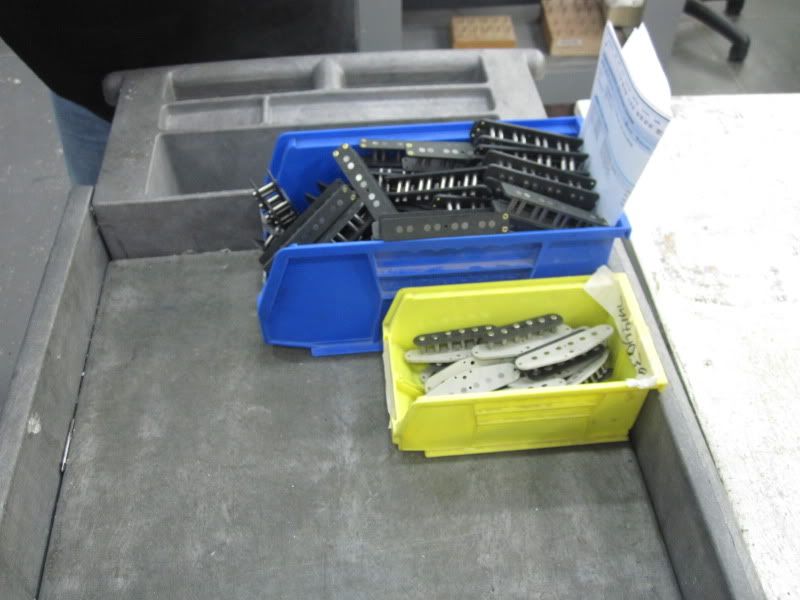
Deluxe reverbs
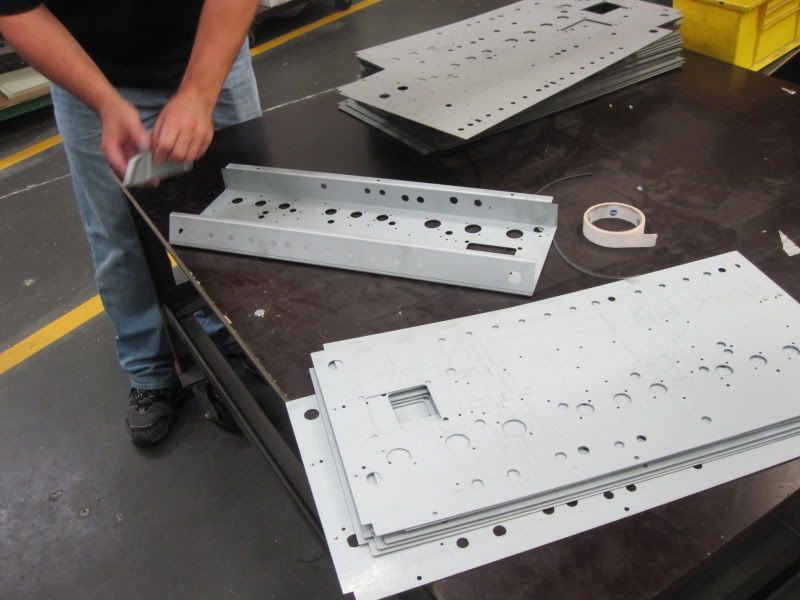
passing by the wood shop
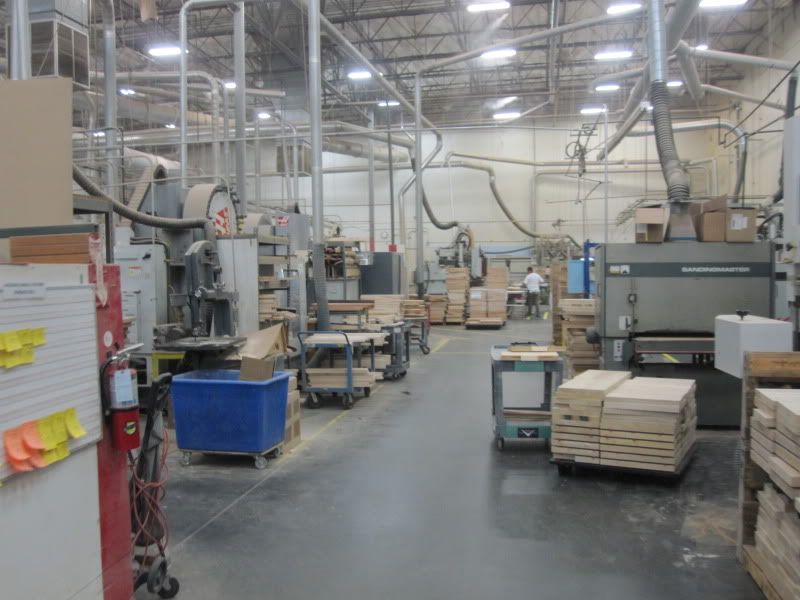
neck blanks
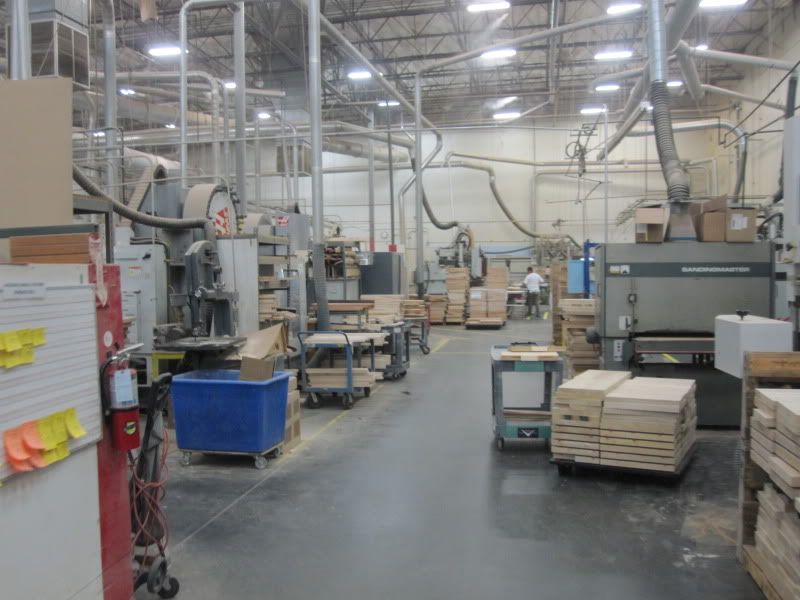
our guide telling how they come with a little bit of milling done
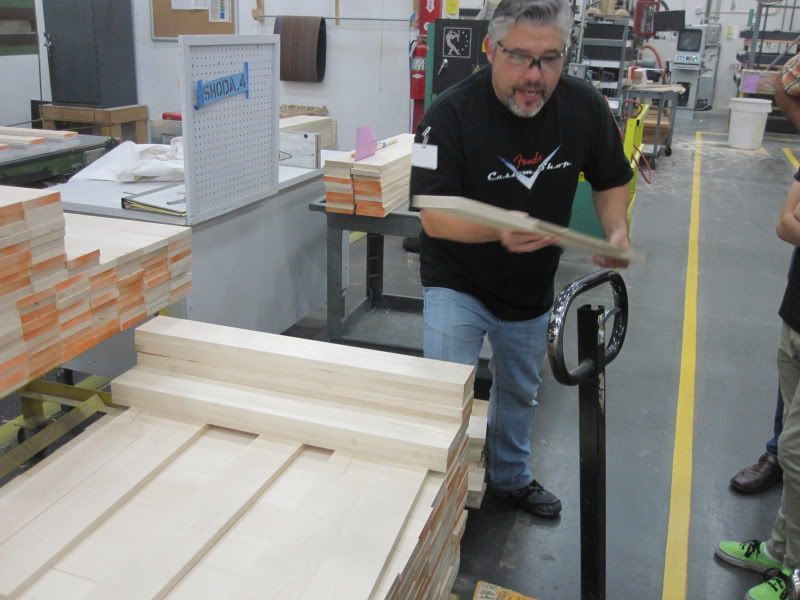
an old style machine that cuts four necks at a time using a physical pattern to copy the cuts for the router. My first tour most of the machines were still like this.
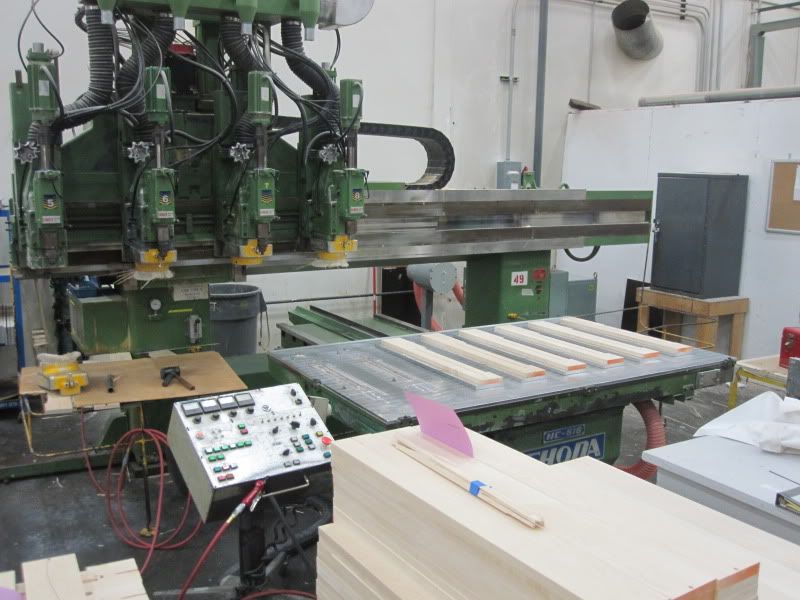
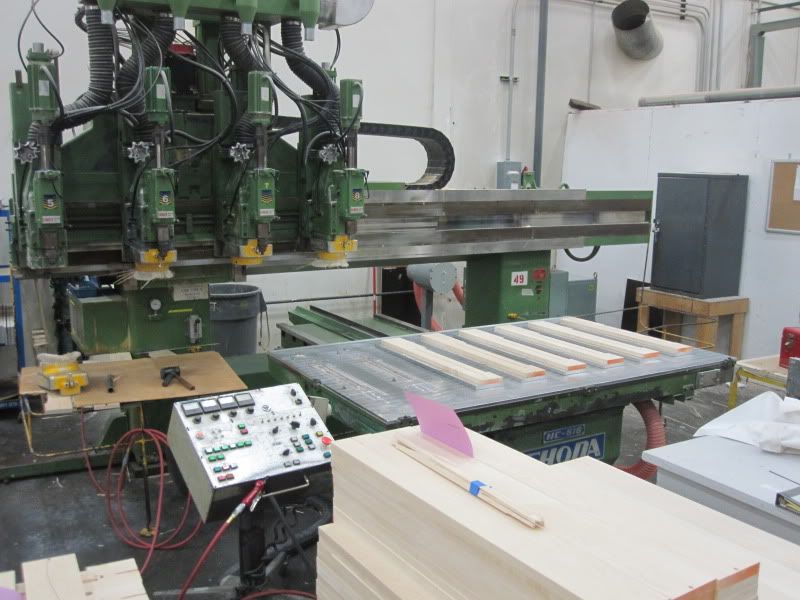
Jacksons
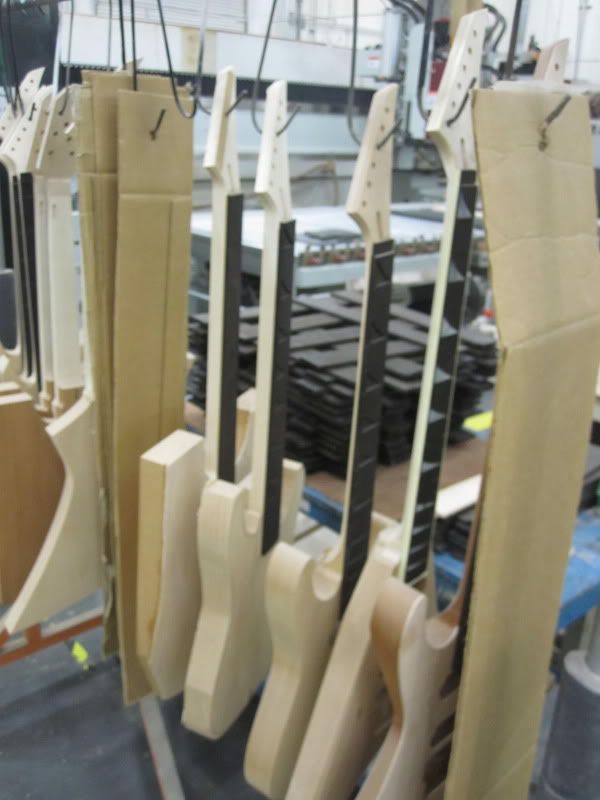
necks getting truss rods and skunk stripes
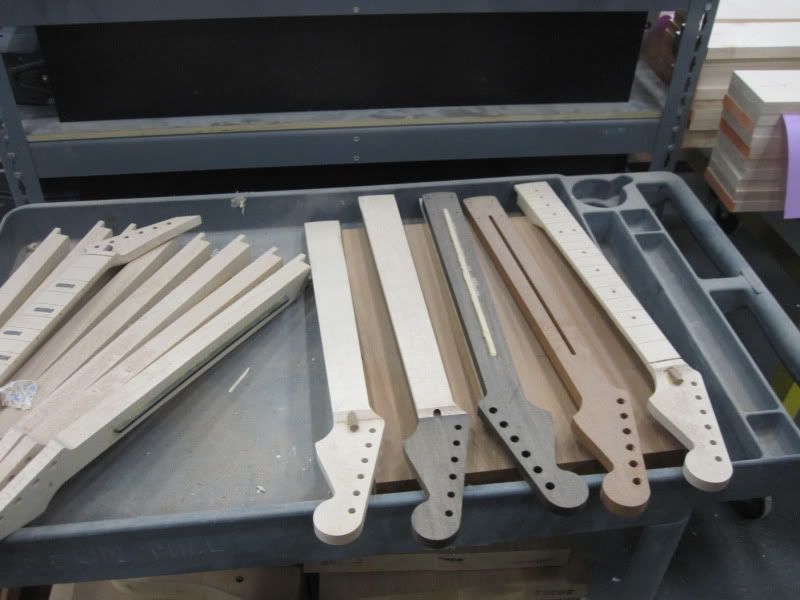
shop fixtures for Jackson guitars
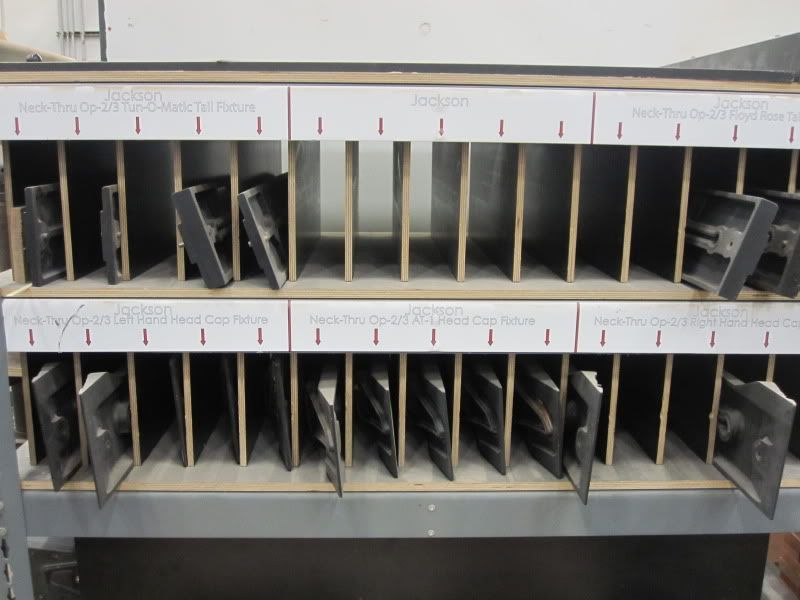
I think these are neck sanders...

installing a skunk stripe
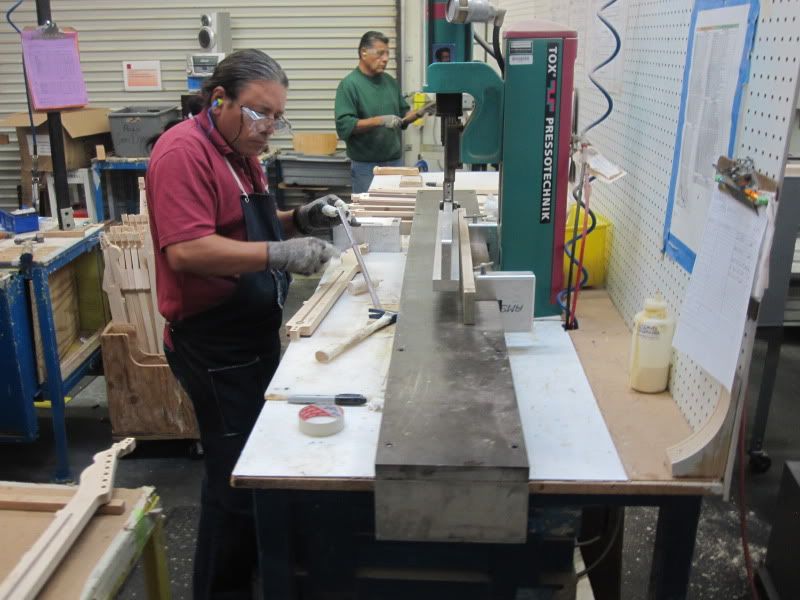
a newer CNC machine cutting necks...this was one of the green pattern following machines the last time I was there IIRC.
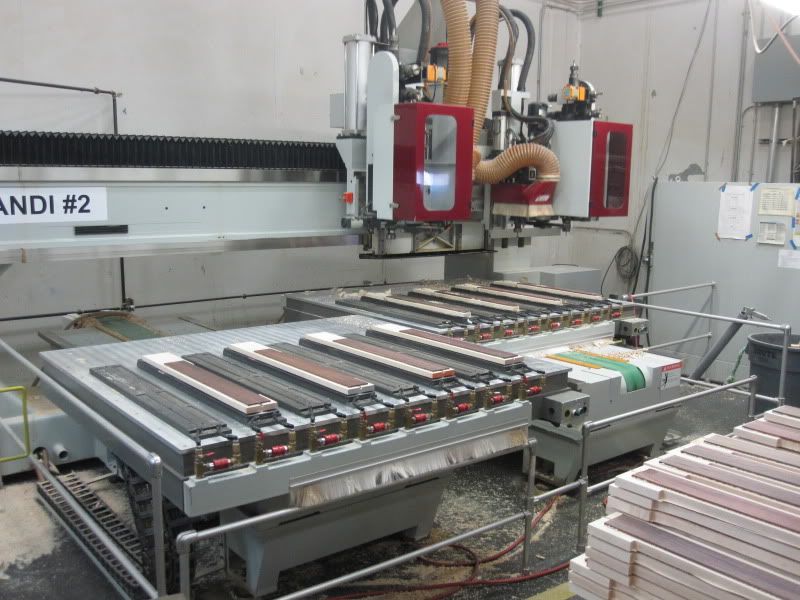